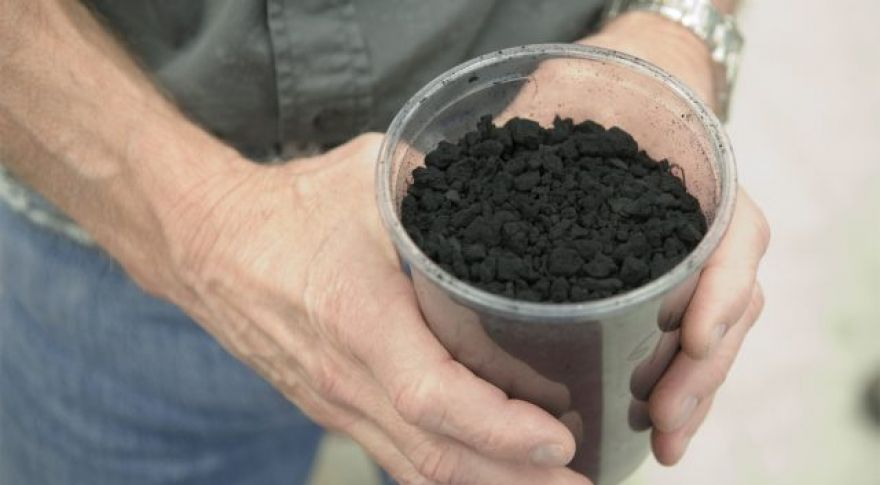
Explosions used to make large quantities of graphene
Graphene was discovered in 2004, and right away its remarkable mechanical and electrical properties made it a hot topic of research. Graphene could be used for super-efficient batteries, solar panels, and much more. But after 13 years, we still don’t have any of that. The problem is that is incredibly difficult to make, but researchers at Kansas State University (KSU) might have stumbled upon a solution. Like all the best science, it involves explosions.
This explosive method for producing graphene was not originally intended to do any such thing. The KSU team was working on creating carbon soot aerosol gels with combustion.
Graphene is a single atom-thick carbon molecule, and the production of it has proven vexing. The earliest samples were isolated from a block of carbon with regular scotch tape, but producing usable amounts of it takes more advanced tools. Other methods involve treating graphite with harsh and expensive chemicals like sulfuric acid, sodium nitrate, potassium permanganate, or hydrazine. It also needs to be heated to at least 1,000 degrees Celsius to get the atoms lined up correctly. The KSU method, on the other hand, requires only hydrocarbon gas, oxygen, and a spark plug.
The process is remarkably simple. The 17-liter aluminum chamber is filled with the mixture of gases, then the spark plug ignites them. The aerosol gel is then collected. It’s extremely low-density, but the chamber produces graphene by the gram rather than by the milligram like other methods.
Since this was all discovered rather by accident, the equipment in use is not ideal for collecting graphene. It currently takes several minutes for the chamber to be safe enough to harvest the graphene gel. With better equipment, the team thinks it could get in there mere seconds after the detonation. This may improve the quality of the graphene that is harvested. This is important because not all graphene is created equal. If a sample isn’t pure, it can take more work to make it usable than it would have taken to just make a pure sample in the first place.
The Kansas team hopes to be able to improve the process to work on an industrial level down the road. The university’s research foundation has been granted a patent on the process.
Now read: